
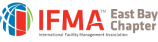
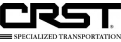
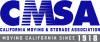
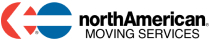
In recent years, the world has undergone a drastic change due to megatrends such as exponential economic growth in developing countries, demographic patterns, and climate. Organizations that intend to keep up with these trends decide to incorporate the latest cost and production strategies. Moreover, an increase in price pressure imposed by customers leads to the production of goods at lower costs.
Continuous cost reduction strategies associated with manufacturing can be done in several ways. Some companies may either replace their machinery or infrastructure with the latest ones or transfer production to low-cost countries. Some enterprises also take over their business partners. Explore how these activities drive the demand for relocation services.
Industrial Relocation and Types
Relocation refers to the complex process that involves site preparation, dismantling heavy equipment, and assembling technical devices in the new location. The process can be divided into two stages – disassembling and reliable relocation service.
There are two basic types of projects when it comes to industrial relocation. The most common one includes dismantling a single piece of machinery when the client has to replace partial infrastructure. On the other hand, a complex industrial plant relocation is less frequent but requires more work and complex planning and preparations to be carried out efficiently.
The process is considered a natural investment for global manufacturing companies to increase and optimize production efficiency. Most often, it’s a primary factor that drives the companies and their production facilities to benefit from globalization and move freely between the chosen locations.
The Growth of Relocation Market
A contemporary business model predominantly improves the production process while a price increase compels companies to look for new locations. These locations can be used as production sites that are beneficial in terms of the company’s budget. That’s why industrial plants are often established in places where production is lucrative, and the local political conditions allow rapid development.
The locational benefits include minimal transportation time and costs because of the proximity to the market or raw materials. The new location may have a greater market size and even better living conditions. The overall cost of doing a business can also be reduced considerably. Some of the regulatory advantages include policy incentives, less stringent controls, tax breaks, and more.
In addition, the lack of adequate space also significantly impacts the decision to relocate the production facility. A bigger space fulfills the need to incur high expenditure on the investment and offers a greater opportunity to expand the plant.
Moreover, merger and acquisition transactions also substantially generate the demand for relocation services, leading to the relocation or sale of non-current assets. The transactions may include those resulting from consolidation trends in various industries.
Since an industrial relocation project involves a high level of complexity, it requires a lot of commitment, ample resources, and a high level of professionalism.
The Need for Industrial Relocation
Industrial relocation occurs when companies need to move an entire plant or heavy machinery. The relocation can also take place from one city or country to another. Its process involves complex planning and begins with the industry’s dismantling – each piece of the machinery is carefully marked and packed.
The next step is usually intermodal transportation via land, air, or sea. Once all the elements are successfully transported, the plant is reassembled, and the operations are resumed.
However, it’s hard to find the relevant information regarding industrial relocation. As a result, entrepreneurs in need of this service are often confused about planning the whole process. They must learn how much time will be required to implement the project and things to do when opting for a relocation company. That’s when industrial movers come in to help industrialists cooperate on their projects.
Not only do they help you plan the entire project, but they also provide dismantling and crane services, transport preparation, loading and transport, re-assembling, and cleanup.
Industrial Relocation Before and After the 2008 Crisis
By the mid of 2007, financial markets worldwide experienced a great recession when banks realized that they would have to bear the losses. Since they didn’t want other bands to give them a worthless mortgage, they stopped lending to each other.
Bear Sterns, the global investment bank in New York City had collapsed during the crisis in 2008. That’s because it was extensively exposed to mortgage-backed securities that transformed into toxic assets as the essential loans began to default.
Before the crisis, the relocation industry operated in a set pattern. The capital-intensive production was relocated (including greater workload, logistics, energy, and legal adjustments) from high-cost countries to developing countries. However, the financial crisis modified the relocation market as companies became more vigilant towards investments’ CAPEX (capital expenditure).
As a result, enterprises now often decide to relocate their facilities and factories again, though they were transferred several years before. The relocation may take place where the headquarters of the company is located. This helps the organization to be closer to its customers and reduce transportation costs.
Relocation decisions are made following a detailed analysis like any other investment project since indicating the most popular destination for industrial plant relocation nowadays is quite difficult.
Diversity of issues accompanied with dismantling and relocation projects is more likely to confuse people who don’t know much about moving an industry. Some of the aspects that require attention include political, legal, and geographical considerations, infrastructure, and culture-related matters.
Selecting the best suitable contractors for this type of service is extremely important from the perspective of timely implementation and the economic effectiveness of the project.
Process of Industrial Relocation
Smoothly carrying out an industrial relocation project requires meticulous planning and precise management to stay within the budget and on schedule. It’s also important to maintain a regulated and safe environment at every step of the process.
Certain protocols to follow include electrical and equipment certification, risk assessment, method statements, lifting guidelines, and individual training. Most importantly, a relocation project can’t be completed without the knowledge and expertise of professional movers.
When relocating an industrial plant, the challenges you’ll encounter are somehow similar to those associated with a residential move. The only difference is that these challenges exist on a larger scale in industrial relocation. Moreover, a mishap during an industrial move could lead to damaged equipment that could sabotage your production schedule.
There’s no room for error in an industrial relocation which is why you must plan every aspect of this project and pay attention to even the smallest detail. If it’s your first experience, you may not know where to begin.
In addition to careful planning, you’re required to coordinate with distributors, vendors, employees, and governmental agencies. You also have to coordinate with utility companies and tech providers to ensure that the new facility is ready for occupancy.
Here’s how you can get all your parts, heavy equipment, machinery, and other materials from one point to another in the most efficient way possible. The checklist below will help you plan your relocation. Though you may need additional steps for your project, the following steps are usually applicable for all kinds of industrial relocation.
- Step 1: Create a Layout of the New Location
Drafting a layout of the new facility will serve as a map for the relocation process. Determine the place for certain machines, storing materials, and inventory. You can also decide where to install the shelving before the transportation.
The layout may undergo several changes. You can also consider having a detailed version of the layout or blueprint of specific areas. Having a layout of the assembly line will provide greater clarity on that area as it serves as the foundation of the rest of the plan.
- Step 2: Review the Equipment and Materials
Carry out an audit for all your machinery, equipment, parts, and other materials to determine where they should be relocated, scrapped, used, or refurbished. You may have a piece of equipment that’s no longer useful. Assess whether it’s worth relocating the equipment or replacing it with a new one.
Outline the cost of moving unused materials and parts in your warehouse. You could also reduce the number of items that need to be packaged and liquidate the rest for some cash.
- Step 3: Create a Relocation and Installation Schedule
During an industrial relocation, the movers can’t drop off everything at once. You need to develop a plan to keep some systems operating in the old facility and start others in the new one as soon as possible. Since the priorities and needs of every business are different, creating a schedule will allow you to minimize the disruption of relocation.
- Step 4: Design The Packaging
Most companies may overlook this step, especially those handling the relocation in-house. Assuming that you only need boxes, cardboard or wood could be wrong and create serious problems. Consider the following questions when determining the packaging for your industrial equipment.
- How vulnerable are your equipment parts?
- How would prolonged moisture or heat affect your products?
- What would happen if the equipment is exposed to vibration during transit?
- Can the equipment be damaged if it hits the container’s side or bangs against other machinery?
- If the machinery or equipment is dismantled, how vulnerable are different pieces?
This is where a specialized team of professionals in industrial packaging serves as a valuable asset. In addition to analyzing your needs, skilled movers can also identify risks associated with dismantling, packing, transporting, and reassembling. They can also design specific boxes and containers to minimize those risks.
To ensure that all the machinery and equipment are safely transported, wooden crates are usually required.
- Step 5: Create Clear Work Instructions
The packaging crew disassembling and packaging the equipment, parts, and other items will need clear instructions. They must know exactly how to package every piece and load it. You don’t want them to make decisions independently and get into trouble. Work with a packaging partner to help you create these plans.
- Step 6: Keep a Record of all Materials, Equipment, and Parts
Before the packaging begins, create an inventory of all your items moving to the new facility. This step will provide you with a mechanism that ensures quality on the receiving end. Without a database or spreadsheet of your listed items, you can’t ensure whether everything has arrived. You must know whether the items are in the same condition they were when packed.
You need to have the technological capabilities to track every package and view the relocation process closely. An industrial moving company will barcode every package that can later be scanned through the relocation. Most industrial movers also use photo documentation technology to evaluate the conditions of all items at each step.
This will help you catch any damage and point it exactly when and where it happened. The right technology ensures transparency and verification to carry out the relocation process successfully.
Types of industrial relocation
Before moving, make sure to choose the relocation process that works best. Here are the basic types of industrial relocation.
- Shutting Down the Entire Operation Until the Relocation is Over
When moving, you assign the last day to take any orders and finish them the day before. On the relocation day, the team will dismantle the factory floor. This may take several days or a few weeks. You won’t have any employees until everything is set.
- Smaller-Scale Production
During this process, you never stop earning money. The movers come and transport the strategic equipment pieces to the new building. You can keep certain parts to fill simpler orders.
- Moving Machinery Overnight
The machinery and equipment not required are moved during the day while the rest can be moved during the night. This allows the company to function throughout the move.
If you’re looking for an industrial relocation service that offers high-quality technological methods, Valley Relocation has got you covered. Our skilled professional movers are trained to carry heavy machinery using cutting-edge equipment. We also specialize in commercial relocation, restaurant relocation, health care facilities relocation, and residential moves. Our services are based in San Jose, Sacramento, and San Francisco.
To learn more about our services, get in touch with us today.